Withstanding the pressure: liners for pressure sewers put to the test
Aging pressure sewer pipes, just like gravity sewers, require renovation. But which methods are best suited for the job? What are the pros and cons of each? The latest IKT comparative product test on pressure sewer liners offers valuable insights.
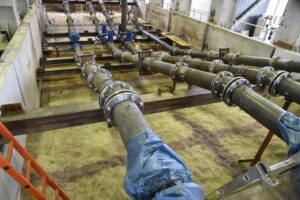
Pressure sewers are critical and sensitive elements of urban wastewater infrastructure. Many are ageing so sewer network owners are increasingly having to deal with their rehabilitation and there are different methods available on the market for this.
Consequently, the neutral, independent and not for profit IKT Institute for Underground Infrastructure, in Germany, has been examining rehabilitation solutions in an extensive comparative product test. Over a three-year period an evaluation project was undertaken on behalf of six municipal network operators from Bottrop, Bremen, Burscheid, Iserlohn, Cologne and Voerde and two regional water associations, the Emschergenossenschaft and the Wupperverband.
The project was supported by the district government of Münster and the State Office for Nature, Environment and Consumer Protection of North Rhine-Westphalia (LANUV). It was financed jointly by the NRW Ministry of the Environment and the eight network operators.
These organisations formed a steering group that determined the pressure sewer damage scenarios to be remedied, the testing programme and the evaluation of the results. IKT developed the test concept, set up the test rigs in its large 1:1 scale test pit and carried out the testing.
Six liners in the comparative product test
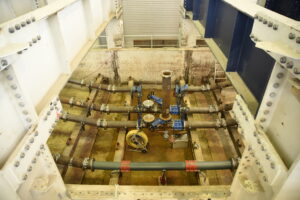
The steering committee selected the following lining technologies for the comparative product test:
Close-fit linier method:
- Compact Pipe (Wavin GmbH)
- egeLiner (egeplast international GmbH)
Cured in Place Pipe (CIPP) liner process:
- Esders HPS Liner (Esders Pipeline Service GmbH)
- Nordiflow WPE (NordiTube Technologies SE)
- SaniPipe (AMEX Sanivar AG)
- Starliner Structure-S (Karl Weiss Technologies GmbH)
Remediation task
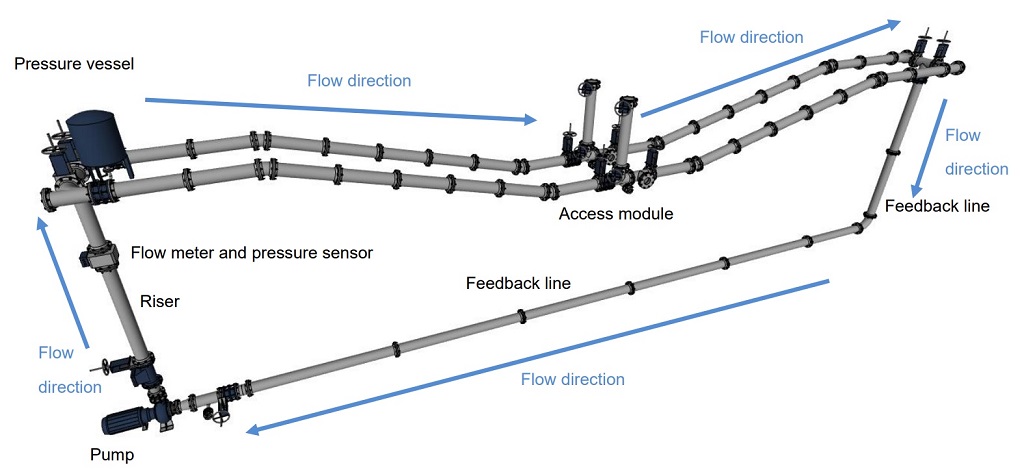
For each liner system, the test setup consisted of a DN200 steel pipe with damage patterns such as holes, leaky connections, point loads, transverse and longitudinal cracks, ovalisation and incrustations. This realistically depicted the damage that network operators find in their pipes.
Class A liner systems
The central issue was whether the liners are suitable as Class A products. A Class A liner must be able to withstand internal and external stresses on its own, regardless of the condition of the host pipe. The stress testing programme conducted as part of the IKT comparative product test went well beyond the regular warranty period of five years in order to consider the entire useful life.
Test program and evaluation scheme
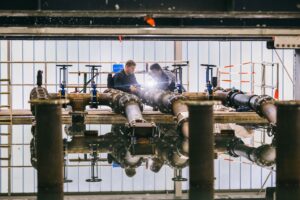
The test programme consists of three phases: The first phase depicted the regular, normal operation of a rehabilitated pressure pipe. Internal water pressures of between 2 and 6 bar were applied at different flow speeds.
In the second phase, the degeneration of the host pipe was simulated over a prolonged period of time. For this purpose, some of the damage scenarios in the host old pipe were worsened in order to simulate progressive damage development and the resulting changes in external influences on the liner. Test pressures and flow rates remained the same as in the first phase.
Finally, the third phase served to simulate additional, non-every day and extraordinary loads on the liner that may occur over the course of its useful life. These included high-pressure cleaning at 80 bar, abrasive substances, the rapid switching on and off of the pump or elevated groundwater levels, such as those that occur when pipes pass under rivers.

Evaluation criteria
The overall grades for the liner systems are made up of the four main criteria of tightness, stability, operational safety and quality assurance. These are divided into nine sub-criteria. The range of grades lies between VERY GOOD (1.0) and INADEQUATE (6.0).
Watertightness criterion (weighting 45%)
The main weak points found in the four CIPP liner processes were the end connections to the host pipe, there were leaks. In contrast, the PE flange and electrofusion sleeve connections of the close-fit liners were reliably watertight.
The close-fit systems Compact Pipe and egeLiner proved to be watertight after renovation. In contrast, the picture for the CIPP liner end connections was very different: Nordiflow and SaniPipe each had to be reworked once to make them all watertight, whilst the Starline end connections had to be reworked twice in order to get them tight. The Esders HPS liner remained leaky even after the connections had been repaired twice and thus it failed on this criterion.
Stability criterion (weighting 25%)
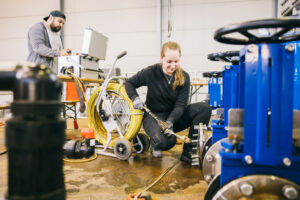
The stability (load-bearing capacity of the structure) was classified by the steering committee as a central “KO” (failure) criterion. It was gratifying that five of the six liner systems tested passed this criterion with GOOD or SATISFACTORY grades. They show no or only minor abnormalities such as local wrinkling.
The SaniPipe liner failed this criterion as it collapsed under external pressure. The reason for this was insufficient fabrication of the liner, which took place without static proof. It was therefore not a Class A liner and consequently received the overall rating INADEQUATE, regardless of performance against all other criteria.
Operational performance criterion (weighting 15%)
This examined to what extent the liners can withstand normal operating conditions such as pressure fluctuations, abrasion, static pressures and high-pressure cleaning.
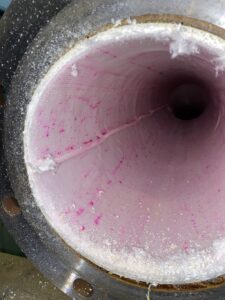
Here, Compact Pipe and egeLiner scored a GOOD grade. Also, they did not form folds and obstacles along their length. However, their installation leads to a hydraulic loss of 6% compared to unlined pipe this was in the middle range. The Nordiflow and Starline liners both had folds larger than 6 mm in the installed liners sheets and thus achieved a SATISFACTORY score. However, the hydraulic power loss of the Nordiflow was particularly high at 8%, whilst the Starline was the lowest at 3%.
With high-pressure cleaning, the Compact Pipe and egeLiner close-fit products achieved a VERY GOOD rating. Nordiflow and Starline withstood this operational stress SATISFACTORILY. On the other hand, Esders and SaniPipe failed this criterion because holes and delaminations occurred. Chemical loads did not have a negative effect on any liner system.
Quality assurance criterion (weighting 15%)
Although all the manufacturers provided an installation procedure manual, some of them have significant deficits in training, test certificates and external and internal monitoring. In addition, the installed Esders and SaniPipe liners each had a continuous longitudinal fold along the length and SaniPipe had design defects, which led to a devaluation of the grade.
Overall result and conclusion
The IKT comparative product test “Renovation process for sewage pressure pipes – Class A liner” confirmed that it is possible to achieve good renovation results. However, there are major differences in the performance of the six rehabilitation technologies examined, which are reflected in the test results awarded. One of the six liners could not qualify as a Class A liner.
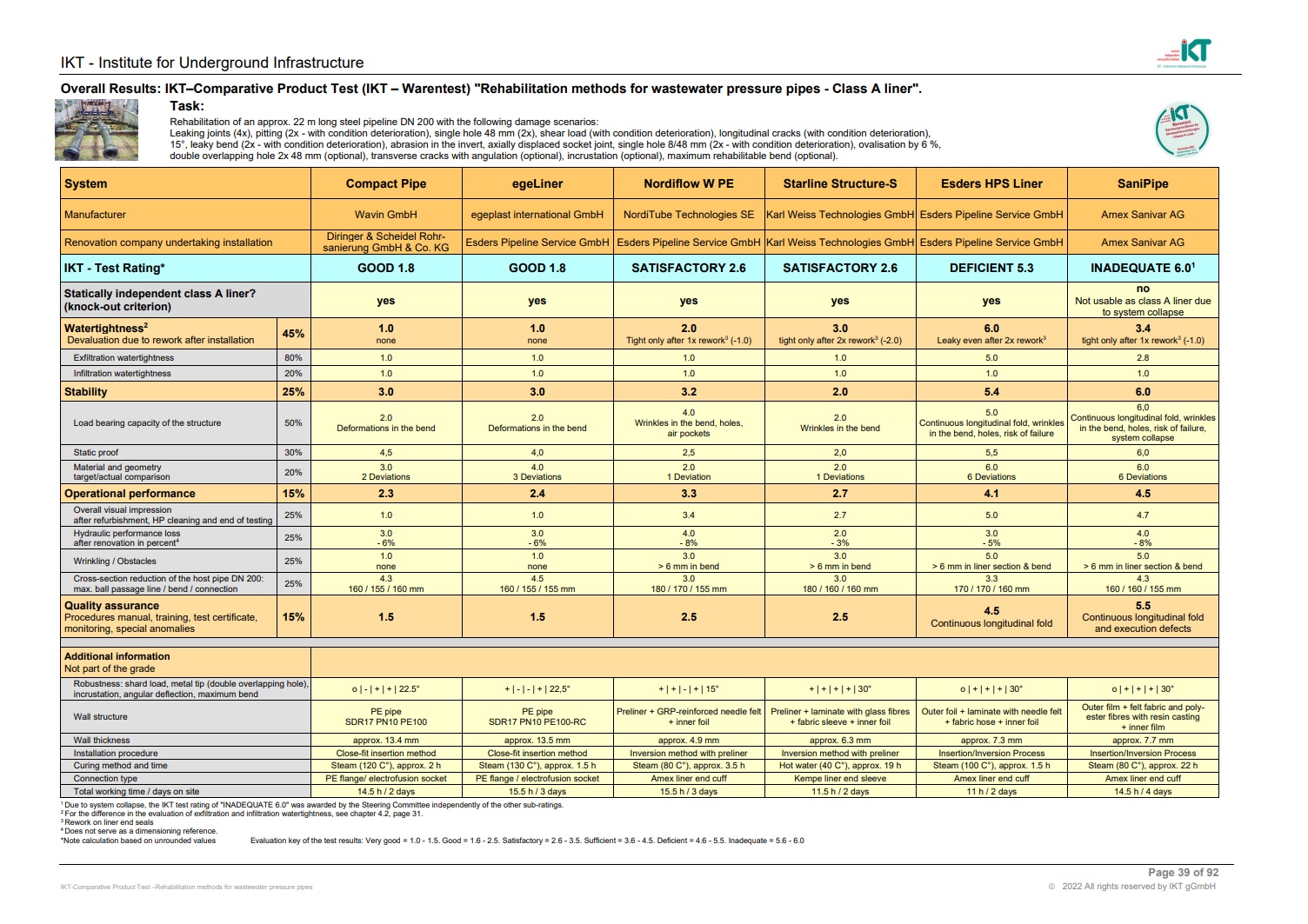
Passed:
- Compact Pipe (Wavin) GOOD (1.8)
- egeLiner (egeplast international) GOOD (1.8)
- Nordiflow W PE (NordiTube Technologies) SATISFACTORY (2.6)
- Starline Structure-S (Karl Weiss Technologies) SATISFACTORY (2.6)
Failed:
- Esders HPS Liner (Esders Pipeline Service) DEFICIENT (5.3)
- SaniPipe (Amex Sanivar) INADEQUATE (6.0)
Results at a glance and complete report (English)
The further deterioration of the condition of the host pipe over time was found to have no effect on the success of the rehabilitation. This applied in particular to signs of corrosion such as simulated pitting and point loads. Only in one case did the complete loss of the supporting host pipe lead to liner failure under external water pressure.
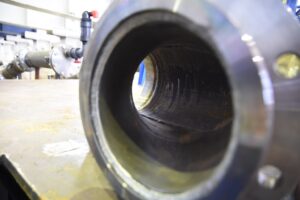
All six of the liner systems could be installed through the four 15° bends included in the rig. Three of the liners were even able to install through a further 30° bend.
The systems were able to withstand normal operating conditions such as pressure fluctuations, abrasion and static pressure without any problems. However, there are clear limits to high-pressure cleaning and holes and delamination can occur here. Chemical stresses did not affect the tightness of the liner.
All liner systems lead to hydraulic performance losses in the pressure sewer the highest up to 8% at the top. The internal diameter was reduced by more than 20% in some places in some liners. Wrinkles >6 mm could be seen on all the CIPP liners. In contrast, the close-fit liners showed no creasing whatsoever, but there was clear ovalisation in the bends.